Automated Optical Inspection Presses Out Defect Inefficiency
Recent technological advances have radically changed the way manufacturers operate. But to truly transform and remain competitive in this industry, more intelligent approaches on the factory floor are necessary.
Chin Fong Machine Industrial, one of the largest metal process machine manufacturers in the world, is seeing this firsthand as it looks for ways to increase its productivity. To produce results, Chin Fong Machine Industrial uses a metal process, a type of equipment that uses manual, pneumatic, hydraulic, servo-electric, and/or other forces to bend and punch holes in metal. They are common in the sheet metal and other industries, and scale from something that could fit on a workbench to the size of a room.
Up until recently, the process of detecting defects in product coming off press machines remained largely a manual one where humans would physically pick up metal sheets and flip or turn them multiple times while visually inspecting the material. Not only has this been inefficient, but it’s also has been difficult to do accurately because of the metal’s reflectivity, varying surface characteristics, and the all the different molds used for pressing.
Which is why in recent years the company has focused on eliminating human defect inspections from press machine production lines.
Compared to human inspectors, automated optical inspection (AOI) systems can dramatically improve productivity and accuracy, and reduce operational costs of defect detection. Moreover, these advanced manufacturing solutions can integrate with machine monitoring solutions like Chin Fong’s iForming Productivity Management System (PMS) software, which allows plant operators to visualize, manage, and act on process data from tens, hundreds, or even thousands of press machines in real time.
AOI systems aren’t new, but they’ve progressed to the point that they can now even spot previously hard to find defected components. These advances are due in large part to recent breakthroughs in AI and computer vision technology.
Compared to human inspectors, #automated optical inspection (AOI) systems can dramatically improve productivity and accuracy, and reduce #operational costs of defect detection. @ASUSUSA via @insightdottech
AI-based AOI: More Than Meets the Eye
Recognizing the capabilities gap, Chin Fong partnered with the AI Solutions business unit of ASUS IoT, a sub-brand of ASUSTeK Computer Inc. ASUS IoT specializes in the design and deployment of embedded system solutions and services that accelerate time to market for companies across a range of vertical markets, including manufacturing automation. ASUS IoT also offers a platform called AISVision, which provides an easy-to-use toolchain and software development kit (SDK) for developing AI model training and inferencing software used in machine vision applications (Figure 1).
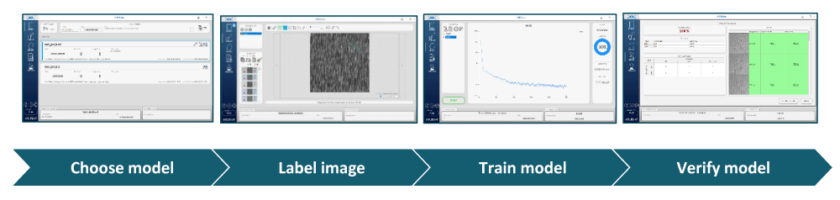
The intuitive, no-code AISVision platform allows domain experts from organizations like Chin Fong Machine Industrial to train machine vision models on small-batch data without having to learn the intricacies of AI itself. It comes with four built-in functions geared toward visual inspection—object identification, multi-object classification, defect detection, and anomaly detection—as well as data filtering features that help users track a model’s effectiveness in different scenarios.
In other words, inspectors and machine operators can train and retrain models using data they’re familiar with to help AOI systems more accurately detect defects like scratches, dirt, and fractures. According to ASUS IoT, it takes only a few minutes for laypersons to familiarize themselves with the platform and just a few minutes more to train models—a process that typically takes at least a few hours.
From there, an AISVision runtime mode serves as an inference engine that can be deployed on edge AOI systems to identify defects and provide more robust field data back into the model training process. Inferencing algorithms generated by the AISVision platform can be executed on several targets, but they perform best on CPUs. In fact, ASUS IoT benchmarks show that anomaly detection and classification inferences perform up to 76% faster running on Intel® Core™ i9 processors than leading GPU alternatives.
These performance gains are possible thanks to AISVision’s reliance on the OpenVINO™ toolkit, an AI model optimizer that compresses and modifies computer vision software for deployment in applications like AOI machine vision. In practice, this enables creation of less-complex, lower-cost, but more-efficient AOI systems.
AI AOI-as-a-Service
Chin Fong Machine Industrial has since outfitted all its metal press products with AOI cameras and lighting hardware, and uses AISVision to develop custom models for clients that are then deployed on that equipment. This ability has transformed a heavy industrial machinery OEM into an end-to-end service provider capable of generating recurring revenue from ongoing model training. Furthermore, predictive insights from the AOI and iForming PMS inform Chin Fong and its customers when components or entire systems must be serviced or replaced—yet another revenue stream.
And all of this while taking human inspectors out of the loop to reduce costs and improve efficiency for customers.
This is an example of Industry 4.0 in action and how a market leader is staying on top in the age of digital transformation.
This article was edited by Christina Cardoza, Associate Editorial Director for insight.tech.