Robotic Arc Welders Detect Defects With AI and CV
Robotic arc welders are the workhorses of the factory floor, fusing steel in the most extreme conditions. As tough as they are, robots can’t QC their work, even when common weld defects such as porosity occur. And when flaws are not caught in the welding process, disruptive and costly rework or scrapping material may be required.
Traditional quality control includes highly skilled weld technicians who use visual and auditory indicators to detect porosity. But these experts are limited in what they can catch. Miles of welds come down the assembly line, making it impossible to visually inspect each one. And they don’t have the ability to see beneath the surface of the weld without radiographic and ultrasonic technologies. As a result, items go out factory doors that can later become warranty claims.
Fortunately, innovative technologies can provide a solution. Robotic welders equipped with AI-driven machine vision can transform quality control and give manufacturers a competitive advantage.
Visual Defect Detection Catches Flaws
The agricultural equipment manufacturer John Deere is a great example. The company uses a gas metal arc process to weld the high-strength steel required to build its machinery. Across 52 factories around the world, hundreds of robotic arms use millions of weld wire pounds annually.
With this tremendous production volume, the company looked for new ways to catch flaws during the welding process. The company turned to ADLINK, a global manufacturer of edge computing solutions.
ADLINK’s AI and computer vision powered Edge Arc Welding Defect Detection solution gives Deere the ability to watch the weld pool in real time to find and correct issues as they occur.
“Machine learning gives John Deere a better understanding of the quality across every single weld,” says Daniel Collins, Senior Director of Edge Solutions for ADLINK. “That is very powerful stuff from a warranty and messaging perspective.”
#ComputerVision and #MachineLearning turn #robotic welders into the superheroes of the #factory floor, spotting defects that would have otherwise gone unnoticed. @adlink_tech via @insightdottech
Rugged Hardware + Pretrained Software
The arc welding platform comprises a combination of software and hardware, based on an industrial-grade machine vision platform using Intel® Core™ processors and Intel® Movidius™ Myriad™ X VPUs.
MeltTools welding cameras—designed to withstand high temperatures and intense light—are mounted on the robotic arm, just 12 to 14 inches from the weld. A pretrained machine learning model uses integrated ADLINK Edge IoT software that can capture, stream, process, understand, and act on vision data. The ADLINK architecture allows manufacturers to plug in modular software and hardware at the edge to create a continuous data flow (Figure 1).
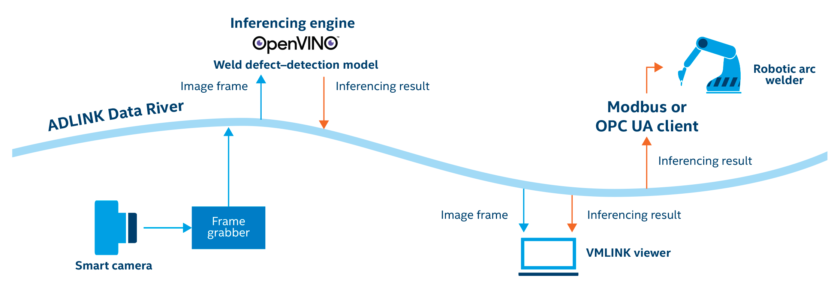
“The software is a big reason why the platform works,” says Collins. “It consists of the Intel® OpenVINO™ Toolkit inference engine, which is the machine vision calculator, and ADLINK Edge, which is broken up into several different applications. These applications do everything from ingest the camera data, stream it to the inference engine, understand the results, and take action. And this all happens in real time using the ADLINK Data River or the Edge communication layer.”
A decision-making app waits for the inference engine’s results to assess the quality of a weld. If it says to stop a weld, a DIO app fires a 24-volt signal to the robot and pauses the weld. At the same time, it sends an alert to the factory floor manager that the weld has been stopped.
“If a quality issue was identified after the fact in a batch, likely they would have to pull all the welds from that batch to further inspect and rework them. That could even mean scrapping entirely and rebuilding from scratch,” says Collins.
AI Brings Business Opportunities to SIs
The robotic arc welding space is growing, and large manufacturers are moving away from manual weld quality practices, which creates a huge opportunity for systems integrators.
“If you do a quick look at what is available from a robotic welding quality inspection perspective, you won’t find much that inspects during the weld job,” Collins says. “You’ll find various components here and there, like cameras and models. What you won’t find are all the components or building blocks bundled together in a single offering.”
Designed for PoCs, the ADLINK kit includes machine vision algorithms that can identify one of the roughly 10 quality inspection issues that are pervasive in welding. To customize the solution for its customer, SIs may need to do some configuration and retraining.
“A customer in a new environment may be able to identify porosity, for example, using the out-of-the-box solution,” says Collins. “Likely however, we would need to do some model retraining to increase the accuracy for that environment. We did the legwork required to identify all the right components. The SI’s job is to configure them in such a way that their client gets immediate value once deployed.”
In addition, many manufacturers are interested in weld quality inspection as a service, adds Collins. “There’s a potential opportunity to offer managed services,” he says. “That, combined with an industry that’s growing and the need to configure and retrain for every customer environment, is quite a bit of services revenue for an SI.”
Computer vision and machine learning turn robotic welders into the superheroes of the factory floor, spotting defects that would have otherwise gone unnoticed. By leveraging AI technology, manufacturers and the SIs that serve them gain an advantage in today’s competitive marketplace.