Farm to Freezer, Real-Time Analytics Cut Food Waste
What if food producers could track their products at every step from the farm to the cold case? More meat and produce would reach the retailer fresh and ready for market. It could also help save the more than 1.2 billion tons of food that due to spoilage never reaches the consumer annually. Innovative cold-chain monitoring solutions can address these challenges.
For example, with meat producers, it starts with healthy livestock. IoT sensors measure environmental conditions such as temperature and humidity. Animal movement, location, and health can be monitored. And the producer is able to take immediate action in unusual situations: relocate livestock, adjust for heat and humidity, even test for illness.
With sensors, AI, and cloud analytics, conditions can be monitored and acted on throughout the supply chain—from transport, to processing, to the cold case.
“A heat wave was pushing one of our customer’s refrigeration units to the limit,” said Ralph Aceves, Vice President of Sales for webee. “The sensors predicted the compressors would likely fail if the weather continued. The customer was alerted and they quickly moved thousands of dollars of meat into another facility, preventing financial loss.”
AI Oversees the Cold-Chain
Webee has developed a Cold-Chain Monitoring solution that simplifies inspection of food across the supply chain. It collects, analyzes, and transmits data, including temperature, humidity, and location in real time, enabling users to make immediate decisions (Figure 1).
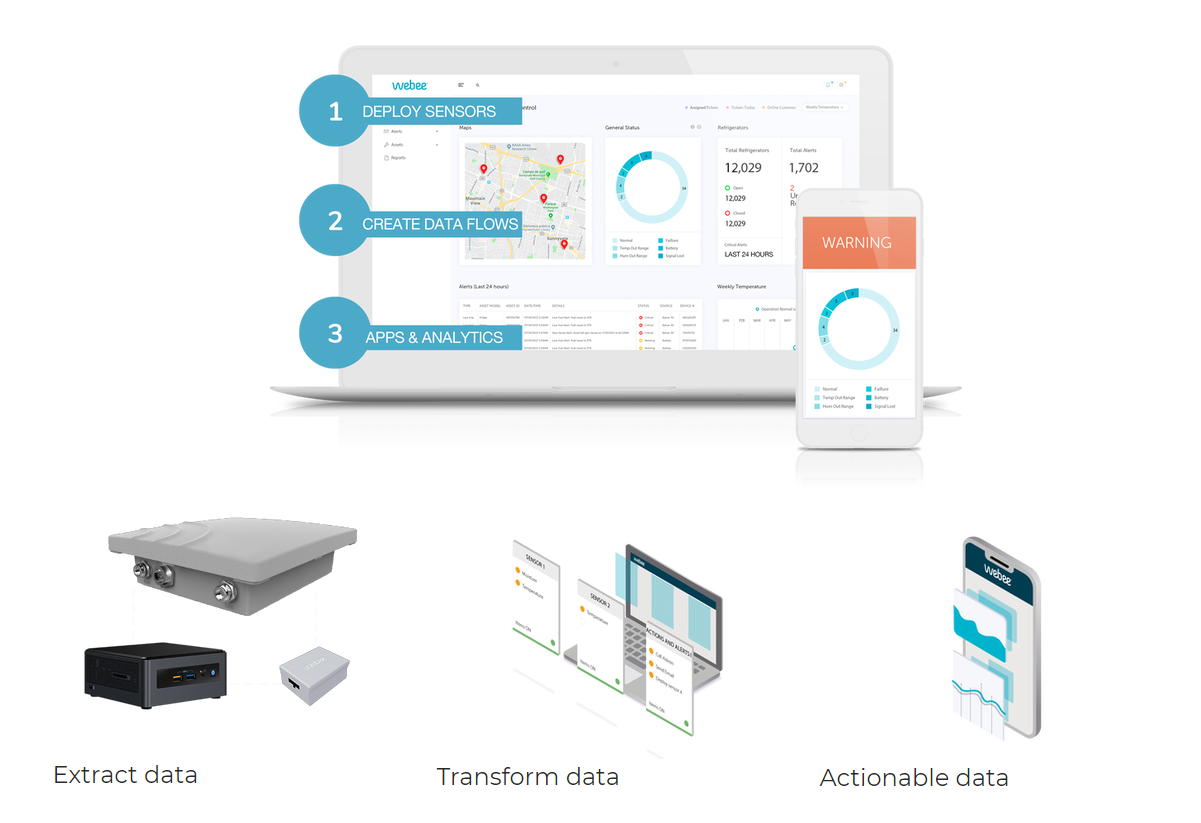
A customer can pre-configure parameters to catch conditions that are unfavorable for food storage. The system can also help prevent false alarms. For instance, a walk-in cold case can be set so that a rise in temperature during delivery times will not trigger an alarm. But if that same rise occurs when the facility is closed, an automated warning will be sent.
“A user can program the solution to send an alert if it detects that a refrigerator door is left open beyond a defined number of minutes,” said Aceves. “Motion sensors will recognize if fragile items such as a pallet of eggs are dropped.”
The system provides real-time temperature, humidity monitoring, and edge analytics across a multi-vendor network. It interfaces via multiple APIs and protocols for integration with CRM, ERP, and other systems. This creates an end-to-end solution to track products throughout transport, distribution, and customer delivery (Video 1).
Video 1. End-to-end temperature and humidity monitoring.
Automating processes such as setting equipment temperature ranges and submitting audit records eliminates the potential of human error. And this simplifies compliance with new federal regulations, which require more critical observation for product temperature audit trails.
“Traditional cold-chain monitoring solutions are out-of-date and require a lot of labor,” said Cecilia Flores, webee Co-Founder. “Our customers want to provide high-quality food and reduce waste. They don’t want to get bogged down with raw information.”
The system dashboard makes it simple to view data and take corrective action as needed. It allows users to push changes to sensors, distribute apps to different users, access historical data, and create alerts (Figure 2).
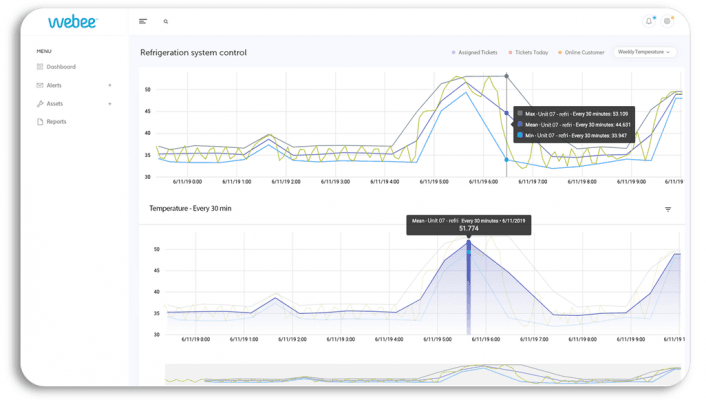
The solution includes an on-premise gateway powered by Intel® technology. Sensors communicate with the gateway via Wi-Fi, ZigBee, or other wireless protocols. Data is backhauled to the cloud over 4G-LTE, 3G, 2G cellular, Ethernet, and LoRa long-range wireless.
The LoRa low-power communication protocol can transmit up to 10 miles line of sight. It extends three miles through buildings, enabling long-range asset management. If there’s a loss in connectivity, webee’s edge sensors continue to collect and send data to the gateway. Once connectivity is reestablished, data is sent in batches to the cloud.
Efficiency is critical. “Default settings on a battery-powered sensor may record and send a temperature reading every 30 seconds, frequently waking the sensor,” said Aceves. “Our solution allows a longer battery life. Users can change the temperature read-and-send from, say, once per minute to every 10 minutes.”
The software is containerized and orchestrated on Kubernetes or Docker. This makes it portable across multiple platforms. And configuration requires no coding expertise. The system automates deploying, scaling, and managing workflows.
Plus, customers can use drag-and-drop applications rather than coding from scratch, making the solution easier to deploy and maintain.
For the future, webee is working with Intel to develop solutions that use computer vision. This will enable the system to recognize and alert users to subtle visual changes such as color and shape. Innovation continues to lower the cost of IoT and other technologies. As a result, cold-chain solutions allow providers to focus on food quality, customer satisfaction, and reducing waste.