Time-Sensitive Networking Opens the Door to Automation
In the transition from conventional to intelligent industrial automation technology, manufacturers must move from operational silos—where systems are separated physically and logically from one another—to a converged, flexible system that can significantly improve operational efficiencies.
Increased interoperability can help fulfill this transition. This will require end users to find new ways to manage disparate systems and solutions so that they can work together. Open platforms, which can host multiple systems and provide an interface between them, will also help manufacturers in this regard.
“Restrictions are a huge pain point for factory owners and machine builders. They’re suffering not only in terms of cost, but in maintenance and engineering,” said Simon Brooks, an IIoT Product Marketing Manager at TTTech. “This type of approach increases complexity in trying to create interoperability between devices from different vendors.”
Another issue to be addressed is data security. For example, access to different data sets must be managed so that proprietary information remains secure. Data and other network connections must also be protected against hackers or other bad actors. This may require provisions for information to remain on-site for local visualization and data analysis.
Reliability is another priority when systems are interconnected and converged. Any solution must be designed to help ensure that performance improvements on one aspect of the system do not hamper performance of another.
Of course, a platform can’t truly provide the benefits of converged functionality if it doesn’t also protect the real-time and safety integrity of critical applications found in factories and power plants.
Real-Time Decision-Making in Industrial Automation
Time-sensitive networking (TSN) offers manufacturers an interoperable network that makes it easier to place intelligence where it’s needed and facilitates converged systems. Organizations such as the Industrial Internet Consortium (IIC), the Avnu Alliance, and others are helping to facilitate a certified networking ecosystem to simplify network synchronization through TSN.
By promoting open standards certification and working to create an interoperable ecosystem that fosters the deployment of low-latency, time-synchronized, highly reliable networked devices, manufacturers can benefit from real-time decision-making in industrial automation. For more information on TSN, see Why Smart Factories Need Time-Sensitive Networking.
The industry appears to be in favor of TSN, and the market is expected to surpass $606 million by 2024. In fact, at the recent Hannover Messe (HMI), TTTech along with a few dozen other companies took part in a TSN testbed set up by the IIC to demonstrate how to use the protocol in factories. See Video 1 for more about the IIC testbed.
“TTTech has been a member of the IIC TSN testbed for several years, and is a leading player in plugfest events,” said Brooks.
The HMI19 demo allowed different, and often competing, companies to come together, test products, and ensure that TSN implementations are fully interoperable. That enabled event attendees considering TSN to experience the full benefits of an open, standard industrial Ethernet.
In addition to open standards, infrastructure should also be able to upload subsets of data to the cloud when latency is not critical to analytics and decision-making. And for truly intelligent industrial automation, the system must also combine elements of both edge and cloud computing.
Edge Puts Computing Where It’s Needed
Manufacturers can use edge computing for intelligent industrial automation, with the Real-Time Machine Data Kit from TTTech offering a compelling use case (Figure 1). This edge computing solution, powered by an Intel Atom® processor E3950, is designed to provide real-time data access, processing, and visualization capabilities for both machine insight and analytics.
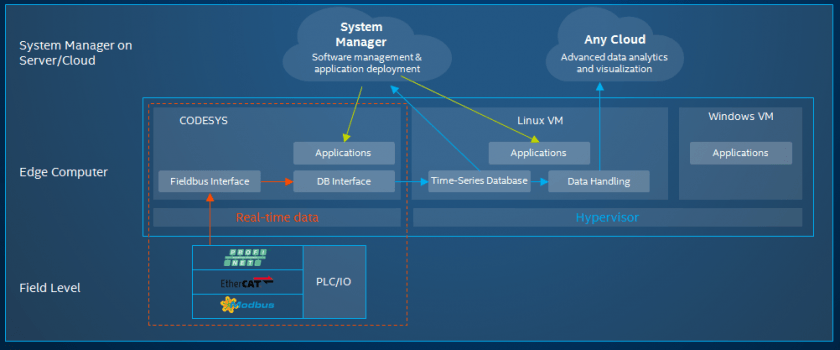
“The Intel Atom E3950 in the Real-time Machine Data Kit allows us to have a small footprint while providing the power to achieve a lot in a virtualized, Industry 4.0 environment,” said Brooks. “That includes solving the synchronization scheduling and interoperability issues.”
It’s also important to note that the kit can help OT overcome the challenge of accessing real-time data from industrial machines without the need to alter existing I/O infrastructure or add gateway devices.
Connecting the kit to industrial I/Os or PLCs enables manufacturers to converge key IoT functions such as data collection, gatewaying, visualization, and application deployment on a single platform. It also allows for connection to sensor/actuator data in millisecond real time via Ethernet-based fieldbuses, like Modbus TCP, PROFINET, or EtherCAT.
Manufacturers also gain an interface that can connect data handling agents to any cloud platform for processing and analysis. And finally, they can virtualize hosting and remote deployment of software applications as virtual machines or in containers.
Virtualization and System Management
Virtualization of compute makes it possible to host applications that can access and process the real-time machine data at the edge. This data can be handled by a time series database, which is hosted in a Linux virtual machine. And for in-depth analysis, data can be uploaded to the cloud via APIs.
Without virtualization, updating machine software is labor-intensive. “You’d have to go to potentially thousands of machines in different locations with a USB stick to run updates,” said Brooks. “That discourages taking advantage of software updates that could increase efficiency, change functionality, or gather and act on predictive maintenance data—all of which can be easily handled with our Data Kit.”
The Kit’s system manager displays an overview of nodes and can be used to consolidate and visualize data from multiple machines across multiple locations. All device software can be remotely managed and updated from a central instance. And, with application deployment, users can introduce new features and functions in Docker containers.
Industrial Automation in a Vendor-Agnostic World
“Our strategy is to reduce complexity for the user,” said Brooks. “Network configuration and scheduling can be challenging, so we’re building products that can interface directly with industrial engineering tools that people are working with today. That way users can avoid engaging directly with the TSN network.”
Another advantage that TTTech brings is vendor neutrality, enabling the Kit to work with any cloud provider and operating system.
As OT is tasked to improve the efficiency of its technology, solutions such as the Real-Time Machine Data Kit from TTTech can help them bring innovation to industrial automation systems. By deploying a converged system that relies on edge computing and time-sensitive networking, manufacturers can improve efficiency and flexibility, and lower costs.