The 5G Factory of the Future with Capgemini
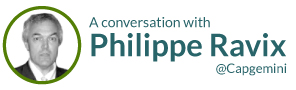
Did you know it is almost impossible to separate 5G and edge computing? 5G is giving a boost to manufacturers’ digital and IoT journeys by eliminating the need for wired connectivity on the shop floor. But it relies on the speed and low latency capabilities from the edge to do so. Together the two power the future of IoT.
In this podcast episode, we explore the challenges facing the manufacturing industry today with the rise of IoT, and the importance of 5G and the edge to address those challenges, and what’s next for 5G and manufacturing.
Our Guest: Capgemini
Our guest this episode is Philippe Ravix, Global Digital Manufacturing Solution Architect at Capgemini, a global leader in digital transformation, technology, and engineering services. In his role, Philippe aims to shape and define the company’s digital manufacturing offering and create an ecosystem of partners in the digital manufacturing and industrial IoT space.
Podcast Topics
Philippe answers our questions about:
- (3:01) The evolution of the manufacturing space since the advent of IoT
- (5:55) The biggest challenges with growing and scaling IoT initiatives
- (7:33) How 5G will play a role in manufacturing’s future
- (10:48) The importance of edge architectures
- (15:02) Complexities that manufacturers are dealing with today
- (26:14) Successfully deploying 5G and edge computing
Related Content
To learn more about this topic, read Moving the Needle to Industry 4.0 with 5G and the Edge and People, Technology Power Machine Uptime. For the latest innovations from Capgemini, follow them on Twitter at @Capgemini and LinkedIn at Capgemini.
Transcript
Kenton Williston: Welcome to the IoT Chat, where we explore the trends that matter for consultants, systems integrators, and end users. I’m Kenton Williston, the Editor-in-Chief of insight.tech.
Every episode I talk to a leading expert about the latest developments in the Internet of Things. Today I’m talking about the impact of 5G on manufacturing with Philippe Ravix, Global Digital Manufacturing Solution Architect at Capgemini.
The way I see it, 5G will be critical to making Industry 4.0 a reality, and it will set us on the path to Industry 5.0. But what’s the right way to adopt 5G in the factory? How should manufacturing processes change in response to this new technology? And what role will edge computing play in all of this? I look forward to hearing how Capgemini is answering these questions.
So, Philippe, welcome to the show.
Philippe Ravix: Thank you, Kenton. Nice to spend time and to discuss with you.
Kenton Williston: So, tell me a little bit about Capgemini and your role there.
Philippe Ravix: So, Capgemini, it’s a huge company—more than a 250,000 people in the world. So, Capgemini is a global system integrator. Capgemini is well known as a global leader in consulting, digital transformation, technology, and engineering services. The group is at the forefront of innovation to address the entire breadth of clients’ opportunities in the evolving world of cloud, digital, and platform.
Within Capgemini I’m VP; I’m part of the global digital manufacturing offering team. I cover Capgemini worldwide. My role is really to define and shape the digital manufacturing offering, and to develop business in digital manufacturing transformation.
To be more precise, my main activities are to define the offering at the group level, to support salespeople during process, to create and develop an ecosystem of a partner—it could be a strategic partner, it could be your local partners—to lead a strategic alliance with Intel®, and to be involved as the solution architect—or CTO—in our key projects.
Kenton Williston: So, just to get a little bit more of your personal history—what did you do before your current role?
Philippe Ravix: I spent my first 10 years in Capgemini working in the IT system as enterprise architect. After this first experience, in fact—so, about 10 years ago—I oriented my career to start a new challenge and work in IoT.
That was the beginning of IoT. I had the opportunity to launch this activity within Capgemini. During this period, in fact, we developed the business in all sectors—like retail, medical device, aerospace, and manufacturing. And we also developed some assets and IPs within Capgemini in collaboration—many with Intel. So, I would say my career is both in the IT system as an architect, and after, now, in the IoT—meaning the IT and OT system, where I work as business developer and solution architect.
Kenton Williston: Certainly a lot has changed in the manufacturing space—which is the topic I want to talk about today. And how do you think the manufacturing space has evolved since the advent of the Internet of Things?
Philippe Ravix: We are now in the digital transformation era, or edge—called also Industry 4.0, factory of the future, or intelligent industry, or smart factory. A lot of terms to express not only that we enter in a data-oriented approach, but in collaboration with the foundation of what is manufacturing—meaning what we call the Golden Triangle based on the three main systems, that is the PLM, the MES, and the ERP.
So the advent of IoT is something that will have an impact on the manufacturing process based on, I will say, data collection, real time, and analytics, and will complement existing systems that are more process oriented, in fact.
So it’s not I will replace, it’s really I will complement and collaborate with the existing systems that manage the shop floor and the manufacturer.
IoT is clearly one of the driving forces behind the Industry 4.0 movement. I think we’ll first enable immense automation. That is one of the key points. First, leverage data collection from the shop floor to the cloud, and at the end, leverage analytics—advanced analytics, in fact.
Why? To optimize workflow and processes inside the manufacturer. So it will be—I will say, today—the next step after the lean strategy, it will be a kind of lean software to have another step of process optimization inside the company and inside the shop floor.
Kenton Williston: Yeah, I agree with that assessment. You’re talking about all the different systems that are involved from an IT side, or from an operations side in the manufacturing sector. You have your PLM, your ERP, your MES—all these systems have an important role to play and, like you said, a big focus over the last couple of decades, really, has been on lean manufacturing.
Although, I have to say the last year or two has exposed some of the flaws in that manufacturing, and we’re still facing a lot of ongoing supply chain challenges. But, nonetheless, moving on to that next stage of a greater level of intelligence I do think is where the future is pointing, and having everything being increasingly data driven, right? That’s really the point of digital transformation. So, I think these are things that pretty much every manufacturer is thinking about, or has embarked on, or has already completed some digital transformation, and is aiming towards this Factory 4.0 regime that we’re heading towards.
But I think there’s still a lot of challenges in this space, and I’m sure you’ve got to see a lot of those firsthand working with your clients. So, what do you see as some of the biggest challenges as manufacturers are trying to grow and scale their IoT initiatives?
Philippe Ravix: For sure there were a lot of challenges for the manufacturers, and where IoT has a, I would say, central role. So, today in the Industry 4.0 there is, I will say, three main challenges, in fact. So, the first one is automation. So, automation is clearly one of the key topics that we see in the market. How we can integrate technologies to automate manufacturing processes?
The next one is flexibility. Flexibility is also clearly something here. In fact, today it takes a long time, if you manufacture a product in the line, you take a long time to change the line, to manufacture another product.
And after, for sure, the sustainability, in fact. So it’s the big trends. In fact, all the clients, all the manufacturers’ industry have this big objective in mind.
In fact, to make the manufacturing cost effective by improving the efficiency of the equipment and processes to minimize the energy consumption; to decrease the manufacturing time, the lead time; to reduce the waste and to use less material. So: automation, flexibility, and the sustainability are the three main challenges that we see.
Kenton Williston: I think there certainly are challenges ahead—not only the technological challenges, but the supply chain challenges I mentioned earlier. A lot of things are changing in this space. And one of the biggest changes—and the key topic I wanted to get to today—was the advent of 5G, which I think is opening up a lot of really exciting new possibilities.
So, can you talk to how you see 5G addressing where manufacturing is going next?
Philippe Ravix: I would say there are two game changers, in fact, today in IoT that will create the IoT of the future. The first one, 5G, is definitely one of the game changers, and edge is the other one, in fact.
So, when I started IoT 10 years ago what it was, it was a device sending data to the cloud for analytics and for human interaction. So it was more cloud to human. So this is a south-north connection from device to cloud, without a lot of data. Now the amount of data, the number of devices deployed, the type of asset connected—for example, in manufacturing if you connect the PLC you should be able to collect data within milliseconds and then 200 parameters. So, at the end of the day you have a lot of data, and you’re not able to send everything to the cloud.
So the edge is really important, and the key part in the architecture and to address this manufacturing challenge—to have this intermediate platform to collect data, to standardize data, to compute data, and after to say: I can send to the cloud, I can send to my colleague, another edge, and so on and so on.
So, edge, it’s quite difficult, I would say, to separate edge and 5G, because 5G—it’s an edge network. So, edge—it’s clearly a game changer for IoT in manufacturing, and it’s something we see now. After, 5G is also, for sure, a key technology for IoT. Why? Because what is interesting with 5G, in fact, is that you will be able to suppress, or to avoid, having wire connectivity in the shop floor.
Meaning, with the capabilities of the edge—meaning speed and near-zero latency—5G will eliminate wire connectivities and will offer a degree of flexibility that I mentioned as a key challenge in the process, by adding mobility for everything.
Kenton Williston: So, it’s wonderful to have this wireless factory that’s so flexible. But then it also means: one, you need to think about where the compute is being done to make the most effective use of those wireless connections. And two, it presents an opportunity to gather so much more data, that you really have to be thoughtful about how to process that data so only the right information is being transported over all of these networks.
So, can you talk a little bit more about the edge architectures you see emerging out of this new paradigm?
Philippe Ravix: So, edge platform is really this intermediate platform that you can have at the device level, you can have at the machine level, you can have at the plant level. So, there are three levels of edge today that we can say each level of edge will have a feature or capabilities for compute and storage. And after, you will say, at the sensor level, at the machine or line level, at the plant level, and after you send to the cloud. And so this is the value of the edge.
The edge is a platform, so it’s 100% a cloud-style architecture. So we can see the edge as part of the cloud—so we do not disconnect the edge to the cloud, or the edge to the cloud. In fact, the edge is seen as part of the cloud—same architecture style—and it’s why the big cloud providers, like Microsoft Azure, AWS, or Google, have now on the market their own edge platforms. Azure Stack, Outposts, or Anthos. So this is why there was an interest from the bigger players in the cloud first.
And with this kind of architecture there was also an interesting point, that today the main connectivity is from device to cloud—so, south to north. With edge, you can create a collaboration from edge to west. So you can create east-to-west connectivity—meaning, edge will be able to discuss and to manage integration and to exchange data from one edge to another one from other specific use cases.
So, everything at the shop-floor level to optimize the process—meaning that you don’t need to send data at the cloud to optimize the process. You can optimize the process at the plant level. So it’s why you have this collaboration between edge and all this data.
One of the key points, also to do this with the edge, is to have this data-standardization feature. One of the key points—that is why it’s quite complex today, because when you collect data from the shop floor, there is a specific model. It could be OPC UA, orif you have Modbus, Profibus, and so on—but it’s always all the protocols. So, protocols first—meaning, that to the OPC UA it’s quite interesting, because you standardize data coming from the shop floor at the device level or at the machine level.
So, very interesting. And after, you send data to the data leg, or somewhere. After—this was the first integration—after, the second integration is how to integrate or to collaborate between PLM, MES, data platform, edge, and so on and so on. That is, specific system with specific data model. But you need to collaborate PLM to ERP and MES for digital continuity, for example. Data platform to MES, for example; to in line quality or process optimization in the shop floor. So there was specific use case for this collaboration and for this, you need to have an integration.
In terms of integration, what happened today in the market, we have more or less integration by the process, integration by the data, integration by the UX/UI. Now, if we can consider that the edge is also able to have a semantic layer, we can add an integration by models directly at the edge level to accelerate the integration between all the systems involved in the manufacturing process—meaning PLM, ERP, MES, and the edge and the data platform.
So, the edge—it’s also the place where you will standardize and create the semantic layer to manage the collaboration and integration between all the systems. So it’s why the edge is so important today in a reference architecture.
Kenton Williston: I can imagine just a whole variety of challenges if a manufacturer will try to do this themselves. So, I would love to get a picture of how Capgemini helps manufacturers actually implement such a system and deal with all these complexities.
Philippe Ravix: The manufacturing is a complex system, for sure, with a lot of complexity from everything—from the connectivity, from the data management, from the data, from the use case, and from the architecture point of view.
So, we support a lot of clients in digital manufacturing transformation. We have a dedicated approach for this, starting both by a business vision and business use cases, and an architecture view. We always start by business and architecture, because in digital transformation there is transformation that is—what is the right use case? What is the value of this use case? And so on and so on. What is the roadmap? But also there is digital—so, meaning that there is the technology. Why? It’s quite impossible, or it would be, I would say, a mistake to separate business from technology today.
So we start to support the client in the business and IT roadmap—I would say that is the first phase. After, we enter in the next phase—that is, depending on the maturity of the client. Because today in the market, most of the big clients’ companies have developed during the last five years, I will say, minimum a lot of proof of concept, proof of value experimentation—I do not know how you can call this. But I will say not hundred, or perhaps sometimes hundred of for proof of concept in digital, for predictive maintenance, for predictive quality, for control, for mobility, and so on and so on.
So, there is a lot of experimentation in each client, and the key problem now is not to identify or to validate the business value; it’s how to scale. This is the challenge today. We know that in IoT we can develop a lot of proof of concept, but the value of IoT is not on the proof of concept that costs money; it’s in the global deployment.
After this business and IT roadmap, we directly go to a scaling program with the client—meaning architecture, so, detailed architecture. And one of the key points is really to have a platform strategy. Do you have the connectivity platform? Which one? Do you have the data platform? Which one? Do you have the analytics platform? Which one? How do you manage the global integration between all the systems? It could be machines, it could be another system based on the semantic layer that is an integration platform, and so and so.
Everything is based on the platform. Everything is based on the cloud-style architecture. So we define this detailed architecture. From the key use cases that have been validated during the phase one or during the previous work done by the client, we select, I would say, a few use cases—no more than five—for development and global deployment. And after we enter in a giant mode with the client.
Kenton Williston: So, we talked earlier about, for example, how the major cloud providers are moving into platforms that go from the cloud to the data center to the edge—and I’ll take Microsoft Azure as the example. So, of course there’s the main Azure platform, which is the cloud platform; but there’s also Azure Stack, which lives in the data center; and the Azure IoT platform, which pushes analytics and all the rest all the way down to the edge, right? So, really important for enabling that east-to-west communication, like you were describing, for providing a level of flexibility for compute and storage networking to be located where it makes the most sense from an architectural perspective.
And then, of course, we’ve talked about all the other systems that are already extant in these plants: you’ve got your SAP systems and your Oracle systems and all the rest. What does Capgemini have in terms of a platform? Or is that part of your offerings?
Philippe Ravix: In Capgemini we have some IPs or assets that we propose as accelerators, as we are a systems integrator—we are not an editor. Most of those industrial assets or IPs have been developed through the Intel Alliance. So, the first one we have, we’re stuck with; it’s an IoT platform that we call XIoT that we have deployed for many clients to manage the connectivity, the wireless connectivity. It could be at the shop floor, but for the distributed assets; so it’s something that we use in the energy for example, in fact, to collect data from the plant. It’s an IoT meter web device management—something that we’ve have had for now around 10 years.
The second one is quite an interesting one. It’s what we call Ensconce. So, it’s a 5G-plus edge platform. It has been developed also in partnership with Intel. So, it’s a 100% pure edge platform that we position in the manufacturing. It’s interesting because it’s both an edge platform and a 5G platform—meaning that we can manage globally the cellular connectivity with the 5G. But also we have the capabilities and features of an edge platform—meaning compute storage. And this platform today is used in many contexts and for many clients too. So, quite a powerful platform to prepare the future, as it’s first an edge platform, and, secondly, it’s a 5G platform. Even today we can use it as a 4G or cellular platform.
Kenton Williston: Just hearing even the name Ensconce gives me some questions. So, when I think of that word, I think of settling down into a secure, sheltered location. And I’m wondering if security is part of that offering. And, just in general, where security factors into your thinking in all of this. Because obviously we’re talking about a much greater level of connectivity, and that connectivity is wireless. So there’s at least the potential there for a much larger surface area for attacks. So what are your thoughts on security? And does that fit into the Ensconce offering, or any of your larger offerings?
Philippe Ravix: So, in the platform that we propose and in the expertise that we can have in 5G, in fact, we manage all the security capabilities inside the platform. So, for Ensconce, we manage their security for the network. For the other connectivity we manage also the security. For example, we manage the encryption with PKU management, for example, between the device and the platform. We manage the security by the IAM identity manager to avoid having an intrusion in one of the systems or one of the machines. And after, we manage the security by the network. But if the network is replaced by your 5G network, we have all the key security features deployed in the platform.
So security can be seen globally in the shop floor. We have this platform, and most of the time in the shop floor we have a private network and we manage the private network in 5G first. And we manage also all the security between the system and machine with encryption, and so on.
And after, on the cloud, we use the security coming from the cloud provider. When we work Azure and AWS—meaning that we know that it’s a secure system—we don’t need to add something. The point is how to manage security between the plant and the cloud. Sometimes we develop some specific network, like what will take place for Azure for Microsoft, for example, or LPN plus secure protocol, HTTPS, and so on.
So we can manage the security from plant to cloud, and inside the plant we manage the security with the network and with the different security topic. So it’s something that we address by design in the solution that we have.
Kenton Williston: Wow, that’s a lot more than I expected. So, we’re glad to see such a heavy focus on security. So, in all of this, how do you work with Intel to achieve success? And how does that relationship with Intel support everything you’re doing?
Philippe Ravix: First, Intel is a strategic partner for Capgemini for many years now. So, in Capgemini we have a global alliance team at the group level. And Intel is part of this global alliance team. So Intel is seen as a strategic partner. So, this alliance is managed at the group level with dedicated organization and governance, and we cover all the geographies or the sectors.
So, now how we work, and what this alliance brings to Capgemini? So, this is first with value for Capgemini. First, because with Intel we know that we will always have the, I will say, the access to the best technologies, to the expertise, and to the innovation. Meaning, with Intel we deliver a lot of webinars, technical sessions, and deep dives in technology or partner technology. Intel brings up the latest technology on cloud, on edge and 5G, reference architecture, and technical support on demand.
So it’s really a technical, or technology, partner that is very powerful, and it’s very powerful in the digital transformation world.
One of the key points also with Intel is that they have a huge ecosystem of partners that is probably powerful for us. And we can access all these partners from Intel. So when we have a question, Intel will be able to put in front of Capgemini the right partners with the right technology, and we can have direct access to the right technology for all projects. So it’s really also a way to accelerate and to secure our delivery.
And, the last point, and very important for us, that we have a joint collaboration in solution development with Intel.
Kenton Williston: So that leads me to my final question, which is, we’ve covered a lot of ground in our conversation today—if you could give manufacturers one key thing they should think about if they’re considering how to deploy 5G and edge computing, what advice would you give them?
Philippe Ravix: Well, if you want success, you need to have a clear vision of where you want to be in terms of business tomorrow. You need to have a clear vision of the market—meaning that if you don’t move, your competitors will move, and you will have lost market share.
So, to be sure that the Industry 4.0 or Industry 5.0—that it’s the next generation with 5G that we’ve got today, if you think we have this Industry 5.0 transformation. But to be sure that the client has a very good understanding of the technology where it is today, and where we want to go tomorrow, and why.
So, first: have this big global strategy at the group level. After, you can start by whatever you want, because more or less we know today what are the best use cases by sector, by industry, discrete process—assembly, packaging, and so on and so on.
Second point: it’s to have the right architecture.
So, meaning the right platform, integrating with the edge—a giant architecture, because everything will move very, very quickly. Second point: so they have a clear view on the architecture and to use the cloud-style architecture. So, the architecture and the way you address the project with the architecture—it’s also a key point. So, the architecture. Because if not, you will have silos.
And after, also to be sure that the client has the foundation of the Industry 3.0; a lot of clients do not have an MES, for example. So, they have an ERP, but they do not have an MES. I just finished a project just to define the requirement for the next MES. And we are in 2021, so, meaning that if you discuss data platform Industry 4.0, you collect a lot of data, and so on and so on, with a client that does not have MES, do not collect data today.
It’s too early. So, meaning that, start by the Industry 3.0. So, it’s why—do you have the right foundation for this? And the right foundation, it’s what we call the Golden Triangle with the PLM, ERP, MES.
Kenton Williston: Yeah. So, a couple of key things that really stand out to me, I think. One is to get to this future you need to start by understanding where you are today. Are you an Industry 3.0? Are you at Industry 4.0—where are you today? And then, two: you have to have a clear vision for where you want to go and buy-in from the individuals at a particular plant that this is the vision we want to pursue, not just something that’s been forced on us. That totally makes sense.
So, with that, I’d just like to say, thank you so much, Philippe, for your time today. This has been a very interesting and engaging conversation.
Philippe Ravix: Thank you very much.
Kenton Williston: And thanks to our listeners for joining us. And to keep up with the latest from Capgemini, follow them on Twitter and on LinkedIn at Capgemini.
If you enjoyed listening, please support us by subscribing and rating us on your favorite podcast app. This has been the IoT chat. We’ll be back next time with more ideas from industry leaders at the forefront of IoT design.
The preceding transcript is provided to ensure accessibility and is intended to accurately capture an informal conversation. The transcript may contain improper uses of trademarked terms and as such should not be used for any other purposes. For more information, please see the Intel® trademark information.