Demystifying Digital Transformation for Manufacturers
The term “digital transformation” has largely been overused and misunderstood, leading many manufacturers to believe they must make huge investments in these efforts. But the point of digital transformation, Industry 4.0, or smart-factory initiatives is to make small but impactful changes that improve operations, performance, and costs.
“You’re trying to increase the efficiency on the plant floor, look for insights, look for ROI, and unlock data,” says Bryan DeBois, Director of Industrial AI at RoviSys, a leading automation and information solutions provider. “How can we use digitalization to make a transformative impact on operations?”
Why Digital Transformation Projects Fail
Many digital transformation efforts fail because organizations try to do too much upfront, DeBois explains.
“Walk before you run. The ones who start small and grow from those are clearly winning,” he says. “There’s a lot of areas that you can find ROI on this digital transformation journey.”
For instance, RoviSys recently helped a disposable-packaging maker automate, collect, and track its production data, providing more insight into downtime and productivity. The packaging maker was using a manual recording process to track data during the production process, resulting in inaccurate or out-of-date information. By just implementing a new data-driven process, the packaging maker was able to increase its uptime by nearly 30%.
“Walk before you run. The ones who start small and grow from those are clearly winning. There’s a lot of areas that you can find ROI on this #DigitalTransformation journey.” —Bryan DeBois, Director of Industrial #AI at @RoviSys via @insightdottech
While it can be possible to “swallow the elephant in one gulp” and do everything all at once, DeBois says that it’s rare and can happen only with 100% leadership buy-in. Leadership buy-in from the top ensures everyone is on the same page and working toward the same goal to improve manufacturing processes.
Much of the operational data necessary to realize areas of improvement is locked on the plant floor. To unlock that data, OT and IT teams must understand each other and work together. It is up to leadership to guide those two parties to the table, help build mutual respect, and provide a collaborative environment.
“The companies that are going about digital transformation right are making sure that OT has a seat at the table right from the beginning and has a voice. We have seen it happen where IT will drive these projects completely without even involving OT, and they’re a failure because OT buy-in can make or break a project,” says DeBois. “IT must recognize that OT is the lifeblood of the company.”
Where to Start Digital Transformation Efforts
Manufacturers know the importance of digital transformation (Figure 1), but it’s not always clear how or where to start. Digital transformation efforts must be tied to a use case or a problem statement from the beginning, DeBois explains.
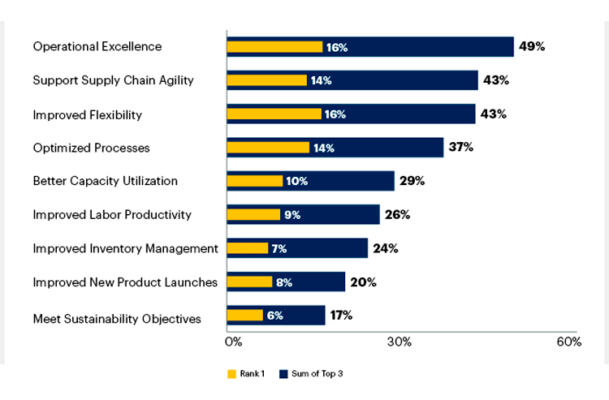
Without a proper use case, the amount of data available can become overwhelming and overload IT systems. By narrowing down the scope, teams can find the right insights from data analytics to solve a particular problem.
Involving an OT System Integrator (SI) like RoviSys early on in projects can help an organization identify its problem areas and build a solution around that.
“We can prioritize use cases, design a solution to solve it, implement that solution, and then support it long term. We can advance the conversation so much faster, and then you can continue to move the conversation forward to get to the higher-value ROI,” says DeBois.
For instance, a recent digital transformation project included an Allen Bradley PLC-5 Control System, which is about 20 years old. The project came to a screeching halt because the team could not figure out how to get data out of the system at a rate that would benefit them. In addition, the system wasn’t scheduled to be replaced for years, and even if it was, it was going to be too expensive to remove.
With its deep manufacturing industry experience and knowledge, RoviSys was able to come in and quickly tweak the PLC’s code to save the entire project.
“One of the things that’s unique about RoviSys is our ability to get tactical. The success of some of these projects is about getting very tactical and getting down to the plant floor, understanding it at a very intimate level, and making sure that everything is set up for success from the beginning,” DeBois says.
Data Guides Implementing the Right Tools for Success
No matter what type of operations a manufacturer has, DeBois explains that once you can access the operational data on the plant floor, it is critical to historicize everything. Historians collect all the data sources coming from the plant floor and put it in a centralized place to visualize, analyze, and diagnose areas of improvement.
An overall equipment effectiveness (OEE) solution can then be added to measure availability, throughput, and quality. “If you can maximize those three factors, you already are going to see huge improvements,” DeBois explains.
An aluminum wheel manufacturer was recently struggling to keep up with the demand for wheels. It needed to figure out how to make more wheels and address throughput. The use case was tied to the saw’s performance.
RoviSys implemented a historian and OEE system to collect information about the saw and operations across multiple manufacturing sites. The manufacturer was able to visualize all the data to compare how different sites were performing or struggling at each phase of the process.
“When you put all of those advantages together between all those different sites, you suddenly could now squeeze more performance out of every single one of those sites,” says DeBois.
Digital transformation efforts can be extended even further with the availability of machine learning and deep-reinforcement learning. These AI models not only help predict value but advise teams on what action they should take next.
RoviSys is one of eight SIs that implement deep-reinforcement learning models from Microsoft’s Project Bonsai. The deep-reinforcement learning models are trained in the Azure cloud and deployed on industrial PCs powered by Intel®.
By leveraging technology and advancements from partners like Microsoft and Intel, RoviSys can provide a complete, holistic manufacturing solution for customers and help guide them toward smart automation manufacturing.
“Eighty percent of the solution typically comes from other software and hardware vendors, and we provide the 20% that makes it one holistic solution across vendors that we can support for customers. Intel has created this great ecosystem for us to be able to do all that,” says DeBois. “They’re pushing the envelope with things like computer vision, OpenVINO™, and chips that are dedicated to AI.”
Manufacturers that have the right partners, have leadership buy-in, tie efforts to a use case, include instrumentation, and achieve IT/OT convergence will see huge success and improvement in their manufacturing systems, according to DeBois.
This article was originally published on September 9, 2021.