Cloud Native Brings Computer Vision to the Critical Edge
At remote oil drilling sites, refineries, landfills, and chemical plants, a flare stack recovery system burns off volatile organic compounds (VOCs). The burning helps relieve pressure from plant equipment, and prevents noxious gases from being released into the atmosphere, where they can damage nearby ecosystems (Figure 1).
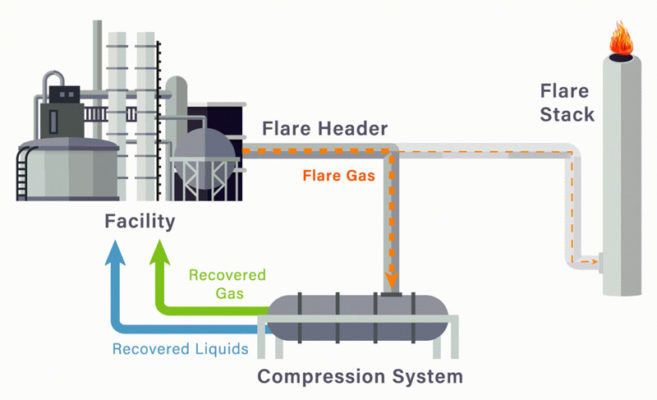
EPA regulations mandate monitoring of flare stacks to ensure that the pilot flame remains lit, prompting use of off-stack thermal cameras outfitted with computer vision (CV) technology. The cameras detect the amount and type of VOCs present in the flame, and the results can serve as lead indicators of pilot flame degradation.
One drawback to this approach is the constant video feed to an analytics platform, which in typical use cases would be in a data center. Such infrastructure is rarely available at remote sites, which leaves operators with two options: either stream the video feeds over a wireless network, or perform video analytics at the edge.
In reality, the cost of streaming video data over a cellular network makes the first option impractical. Simply put, video analytics must take place at the edge, which presents challenges of its own:
- The software, algorithms, and storage required often far exceed computing resources available at the edge, which requires additional equipment.
- This equipment will likely come in the form of a server, which must meet industry standards for deployment in explosive environmental conditions.
- The system must be able to integrate with on-site HMIs, networks, and SCADA infrastructure so that action can be taken immediately if a fault is recognized.
And those are just the initial complications of edge-based video analytics. Because of inherent security concerns in these use cases and the operational background of engineering staff, there is reluctance to deploy IoT and cloud technology in remote plants.
This makes the other big problem just getting out there.
“The challenge of deploying computer vision solutions at scale in the field is not new. Typically a technician drives out and installs cameras connected to a server or PC in a closet. After that they never see them again,” explains Jason Shepherd, VP of Ecosystems at ZEDEDA. “They turn it on and start recording. All the data is stored locally, and if something happens, an operator can look at the footage, which has a 2-week to 30-day retention. They have remote visibility into whether that box is running.”
And if operators determine that something is wrong with the video system, or if it needs a simple software update?
“They’re often using SSH to get into the box and update things manually,” Shepherd adds. “If you have to do that 50 times, 100 times, it’s very painful, and not scalable.”
Multiple containers housing applications like CV, analytics, and security can be deployed on a single edge server, and managed remotely from the cloud.
Video Analytics at the Edge: Seeing through Legacy
But rather than bending the enterprise technology to the operational context, why not bend the operational context to the enterprise? After all, the technology is far more advanced than the legacy installed base of electronics at the edge. And, more important, it enables cost synergies through workload consolidation.
ZEDEDA, a provider of IoT and edge computing services, is enabling computer vision at the edge with a cloud-based, hardware-agnostic IoT edge orchestration solution for precisely these use cases (Figure 2). Built on the Edge Virtualization Engine (EVE), an open-source project hosted under the Linux Foundation’s LF Edge umbrella, the system allows users to consolidate existing and new applications in Virtual Machines (VMs) and Docker containers. Legacy applications in VMs and containers housing modern applications like CV, analytics, and security can then be deployed on a single edge server, and managed remotely from the cloud.
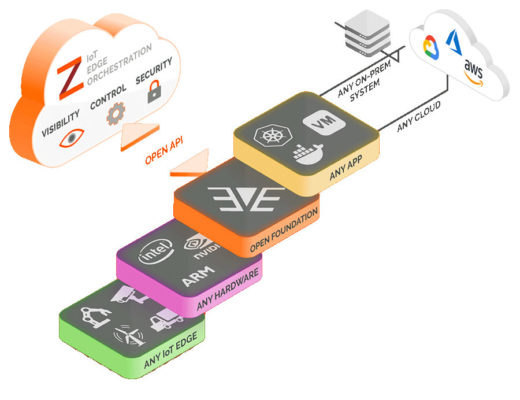
In mixed-criticality use cases like flare detection and monitoring, the EVE foundation supports the open-source ACRN hypervisor as an option to safely and securely partition containers running regulated applications from other software components. This architecture ensures that processes from different applications do not interfere with one another, and bugs or vulnerabilities are contained there.
The solution also comes in handy when performing over-the-air software updates.
“If you have a legacy SCADA system or are using OSIsoft PI as a historian, but want to consolidate that on a server alongside a modern app like an AI model in a container next to it, we can support that,” Shepherd says. “It’s bare metal, so we can do all kinds of stuff around security and networking, and we can assign certain cores of the CPU to certain apps.”
“When the system is able to phone home, it tries to update on a separate partition. If it doesn’t update successfully in about 10 minutes, it falls back to the version it was running before the update began,” he continues. “It’s also designed for the edge node to run autonomously if the connection is lost. That is not how it works in the data center. They count on a really good pipe from the controller to the data center. We count on not having that.”
Plus ZEDEDA supports zero-touch provisioning that allows operational engineers to onboard devices seamlessly so there’s no IT learning curve.
Flare Stack Monitoring, from Prototyping to the Plant
To support specific use cases like flare stack monitoring, ZEDEDA hosts an “app marketplace” of software, certified to work with the platform. These include protocol conversion stacks, APIs for integrating with cloud platforms like Microsoft Azure IoT Edge, and deep learning-based CV models. Also supported is the Intel® OpenVINO™ Toolkit, which helps optimize AI algorithms to run on Intel® processors.
The company’s Edge AI & Computer Vision Acceleration Kit assists industrial operators in combining these and other components into a working end solution for applications. The technology stack resembles one used by a major oilfield services provider, which leverages ZEDEDA’s implementation of EVE to deploy and manage FogHorn Systems’ deep learning-based flare stack monitoring CV software at remote oil drilling sites.
Openness and Opportunity for Industry
As cloud-based technologies become mature enough for use at the operational edge, industrial organizations that have been reluctant to mix enterprise and embedded infrastructure will begin to see opportunity in these hybrid designs. And a significant amount of hardware can be consolidated onto a single server that runs multiple apps, which reduces capital expense, operating expense, and points of failure. But there are additional benefits.
Because ZEDEDA is built almost entirely on open technologies, industries that have been mired in proprietary technologies and vendor lock-in now have alternatives.
“EVE is all about taking the best of the best industry standards,” Shepherd says. “We’re working with platforms like Kubernetes, ACRN, KVM, Xen, and Intel® Secure Device Onboard and packaging it together. Then we build that cloud controller, making it easier for operators and service providers to deploy.”