Case Study: NASCAR Engines Roar with AI and ML
In the world of NASCAR racing, fractions of a second count. And that’s not just during a race—it also applies to development and testing of high-performance engines.
And when you consider the precision required in industrial asset maintenance applications, there’s a lot to learn from NASCAR engineers. For manufacturers and the systems integrators (SIs) who serve them, automating the operation and maintenance of expensive machines can boost productivity and cut downtime on the factory floor by orders of magnitude.
NASCAR has established strict rules about the size and specifications of a legal racing engine. Still, almost every engine is built from the ground up to deliver slight advantages in powerbands, torque, etc. It’s a time- and resource-intensive endeavor, where an engine can cost $250,000.
Given this expense and the grave dangers of an engine malfunction, NASCAR teams exhaustively test engines before they make it to the racetrack. Test engineers intentionally push these systems to their physical limits to identify component degradation, microscopic structural damage, and other potential causes of failure.
Using this “forensic evidence,” racing teams can understand how best to run the engine to minimize failure and rebuild portions with more robust parts if necessary. But capturing this data means stopping the test procedure fractions of a second before catastrophic failure.
For years, these processes have been almost entirely manual. But now one racing team is empowering test engineers with IoT edge compute to capture data, analyze it, and terminate the test at the last possible moment.
Real-World Simulation
The team uses a system called a dynamometer, or dyno, to test its engines. Dynos simultaneously measure engine RPMs and torque to provide insight into its power, calibration of engine management controllers, or, in this case, combustion behavior (Video 1).
A 1,000-horsepower electric motor is connected to the engine and dyno testbench. This motor can be used to exercise the entire engine or perform individual unit tests on components like valve assemblies.
Real-world telemetry data from races like the Daytona 500 can then be used to control the test. Alternatively, RPMs can be ramped up, down, or held at some predefined level for a period of time that push the engine or components to extremes.
After a sufficient battery of tests are performed, engineers from the racing team often intentionally test engines to the point of destruction. When testing for combustible behavior and the resulting forensic evidence, the testbench is placed in a blast chamber with bulletproof glass to protect engineers in case the engine explodes.
In a traditional test environment, highly skilled engineers monitor these digital samples while also listening for subtle changes in engine noise that can signify an imminent explosion. Test engineers usually have only 1.5 seconds to recognize and react to these changes—hitting a kill switch to prevent the engine from being destroyed.
When an engine under test remains intact, engineers can deconstruct it, look for evidence, and attempt to correct issues. If they fail to stop the engine in time, the vast majority of this information will be lost.
Where things become really interesting is when domain experts (like the @NASCAR engineers) use automated CM systems to develop AI and machine learning models. @adlink_iot @insightdottech
Automation with AI and ML
Automated condition monitoring (CM) can be extremely effective in these scenarios because of the vast amount of data that can be collected and analyzed in real time. CM systems fuse testbench data from multiple sources such as flow, pressure, temperature, vibration, and acoustic sensors. And they can also clean sensor data by removing noise or interpolating missing values.
But where things become really interesting is when domain experts like the NASCAR engineers use automated CM systems to develop artificial intelligence (AI) and machine learning (ML) models. These models can be trained to understand what sensor readings are predicting in terms of machine health and potential failure. If certain factors are met, the CM system can alert the engineer with greater accuracy and consistency to kill the engine immediately or even trigger an automated kill switch.
To help automate test procedures, NASCAR engineers needed a high-performance platform. But the end solution had to be compact and rugged enough to hold up in a garage environment.
The team selected the MCM-100 Machine Condition Monitoring Edge Platform from ADLINK Technology (Figure 1). Not only did the system meet their harsh setting requirements, it was installed and sampling data in the racing team’s garage in under an hour.
The MCM, combined with a smart camera and ADLINK Edge software, lets the team apply machine learning and reliably diagnose problems, understand failure modes, and avoid engine damage. For example, the solution enables real-time, secure data streaming from devices and sensors monitoring vibration and acoustic emissions. Data is then aggregated at the edge.
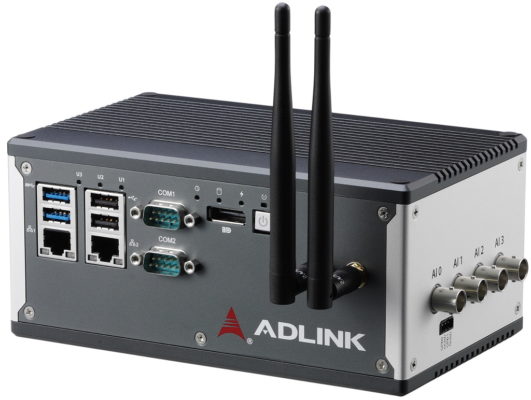
Based on the Intel Atom® x7-E3950 processor, it supports four channels of 24-bit 128 kS/s simultaneous data sampling—meeting the specs for machine vibration measurement. It delivers edge-based data acquisition, analytics, and domain-specific algorithm execution for real-time monitoring and control of the engine testbench.
In the new setup, Ethernet cable runs from the testbench, out of the blast chamber, and into another system before connecting to the MCM-100. The intermediate system is also bridged onto the racing team’s Wi-Fi network, making it possible to pipe test data into the cloud for storage and retrospective analysis.
But the real value is found at the edge—where the data is generated and analyzed in real time for speedier insight and action. This is enabled by the ADLINK Edge software, which is pre-installed on the MCM-100.
Prior to the MCM-100, the team used SCADA systems to monitor their sensors. But there was no need to rip and replace any legacy equipment. The ADLINK Edge software integrates data from existing and new devices. The system is based on the Data Distribution Service (DDS) networking middleware, which helps liberate data in siloed architectures so that it can be applied in real time to applications like high-performance engine testing.
Better Tools Win the Race
It’s important to note that the solution presented here doesn’t replace test engineers; rather, it relies on their expertise to achieve optimal results. Thus, the system can detect warning signals and respond faster than humans—helping protect investments and bring better engines to the track.
“Much of what we do is about augmenting humans, giving them better tools,” said Joe Speed, Field CTO for Global Partners at ADLINK.
And these tools can augment an SI’s business, too. With solutions like the MCM-100, savvy SIs can engage their customers in new ways and over longer time periods with a “machine maintenance-as-a-service” business model.
Add the value that solutions aggregators can bring—IoT education, the technology itself, and a reliable network of partners—and SIs can source all that they need to take advantage of this important opportunity.
For this NASCAR racing team, the combination of domain experts, AI, and machine learning is helping push engines through the checkered flag faster than ever. It will help SIs win the race, too.