AI and ML Automate Visual Quality Inspection
Developing industrial AI-enabled applications from the ground up is a big challenge. But using a recipe-like approach makes the process easier. What does that look like? It includes a list of ingredients containing IT and OT hardware, the software to tie them together, and a selection of pre-built algorithms. It also provides directions, like how to leverage cloud services and tools—even how to automate provisioning and deployment. And like a great recipe, this approach lets you substitute ingredients to customize your applications.
Smart factory visual quality inspection applications are well suited to this method. That’s because no matter what’s being manufactured, the solution identifies anomalies before they occur. It does this by comparing what’s happening at different points on the production line against a library of data.
This enables the system to automatically determine when and where a manufacturing process is beginning to slip out of spec—enabling corrections to occur before quality suffers.
Designing a Visual Quality Inspection Solution
A recipe approach offers developers several benefits. Foremost, by using a formula, it gives them the confidence to take on comprehensive visual quality projects for a variety of manufacturing sectors.
It requires matching various KPIs along a production line with sensors that measure them. Sensors may include video or still cameras for computer vision as well as instruments that gauge vibration, temperature, and other data. From there, a developer applies machine learning algorithms that sense impending problems on the production line.
Such a solution allows parts or goods that pass inspection to move on, while those that fail are reworked before leaving the factory. This helps eliminate the need to scrap material (Figure 1).
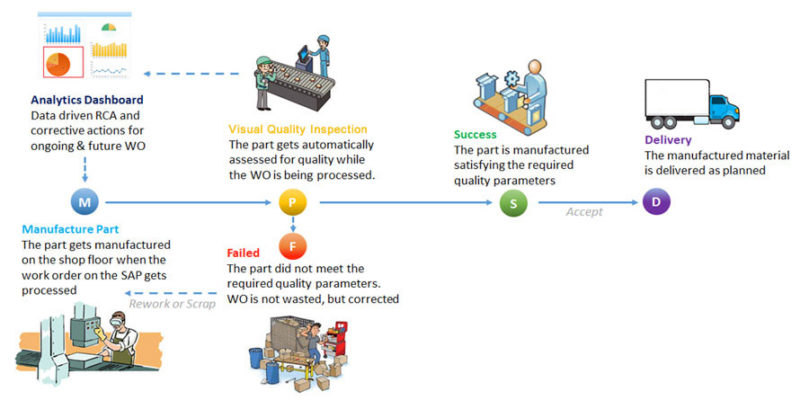
“Collecting and processing data in real time calls for sophisticated analytic models to automate quality control,” said Fabio Terasaka, product manager at Hitachi Vantara, a Hitachi subsidiary that supports developers building IIoT solutions.
Terasaka described how two different sectors deploy different visual quality inspection solutions. “A food and beverage manufacturer could automate smell-detection to determine if their ingredients are fresh or near the end of their shelf life,” he explained. “Or a discrete manufacturer could automate tracking visual alignment of parts or labels. If the position slightly alters, it’s likely that a machine must be recalibrated.”
To help developers build an inspection solution, the Hitachi Vantara solution enables them to use familiar tools such as elements from the Google Cloud machine learning platform. This includes IoT Core for data ingestion, AutoML for machine learning, inference training and data processing, and web servers for storage and visualization and other services.
“We’ve worked on some strategic projects with Google,” said Terasaka, “where their engineers provide AI and machine learning expertise that complements our customers’ in-house SMEs.”
To simplify development, the recipe calls for Intel® gateways and cameras, which enable AI applications to process image data at the edge on the Intel® NUC or other devices. It also supports TensorFlow and the Linux operating system, making it user-friendly.
Developers may also choose software and algorithms based on application needs, for instance, establishing connectivity to industrial assets running on proprietary industrial protocols. This requires a gateway that translates a proprietary format to something more common, like MQTT or AMQP.
With high-throughput processes, visual quality inspection might capture and analyze nearly 100 images in two seconds.
@HitachiVantara
AI Technology, Performance, and Comprehensiveness
When speed is necessary, things happen faster than the human eye can detect. In high-throughput processes, visual quality inspection might capture and analyze nearly 100 images in one or two seconds. It may also need to recognize imperfections at the micron level. This calls for automation and high resolution, combined with low-latency computer vision.
To illustrate, Terasaka described a company that makes 1,400 pistons an hour, which requires continuous inspection at multiple points: “When things go wrong, automation is the only way to detect and take corrective action—avoiding a large volume of scrap and rework.”
Depending on the use case, LiDAR (Light Detection and Ranging) makes a worthwhile addition to a comprehensive visual inspection solution. The technology can record the position of workers in a factory. “It measures the correlation between the movement of a machine operator and product quality, as well as helps ensure safety,” said Terasaka.
LiDAR can also be used to alert if an operator dropped a part, picked it up off the floor, and put it back in the line or placed it in a bin for re-inspection.
Monitoring machine health is another solution benefit. For instance, by slowing down a process, a factory may not only increase output of high-quality goods and reduce waste, it may avoid shutting down a production line to fix equipment.
Applying additional data streams to these solutions provides further advantages. For example, an ERP interface may help answer questions such as:
- Do quality issues continually arise with material or parts from a specific supplier?
- At what point will scrap prevent or delay delivery on a customer’s order?
- Can a maintenance schedule be reevaluated based on scrap and waste?
Growth in Smart Factory Development
Hitachi’s own manufacturing experience has shaped the way it advises developers to follow its recipe approach. “It’s helped us bring together those in IT and OT, as well as our partners like Intel®, to build efficient quality solutions,” said Terasaka.
“By commoditizing machine learning technologies, our end customers can get a visual quality inspection application up and running without building it from scratch,” Terasaka added. “Better yet, this approach helps developers build these types of use cases for almost any industry.”